Don’t let changes on your shop floor
trip you up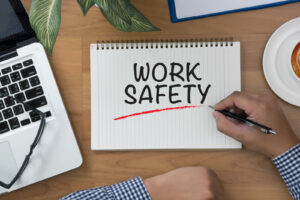
Almost all businesses will have to consider visitors on their premises as well as employees, when assessing health and safety risks. But if you run a shop, or group of stores, and you are hoping for a large customer footfall, understanding the risks to the public will take on heightened importance. When they are getting some retail therapy, or picking up a few essentials, your customers will expect to be safe.
Local authorities enforce health and safety law on retail premises, and they will expect you to have assessed the risks in your business and taken precautions to manage them. Bear in mind, as you will see below, that this is not a one-off exercise.
The most common risk to customers in retail is of slips, trips and falls, so this must be properly assessed and controlled. Wet or dirty floors, spillages, damaged floors and other trip hazards are the most likely causes of an accident, but your business might have its own particular risks too.
Other health and safety considerations that are likely to be relevant to retail include manual handling, violence, working at height (if ladders are used), and workplace transport e.g. deliveries.
And then there are the hazards that are very specific to your store. Be especially aware when you introduce new equipment, fixtures, furniture or furnishings to your shop floor. Even though a change may be ad hoc, it’s essential to update your risk assessment.
In January 2019, the owners of Top Shop, Arcadia, were fined £450,000 when part of a queuing system barrier fell on a ten-year-old girl and fractured her skull. The barrier was successfully used in flagship stores but had been deployed to a smaller store which were not accustomed to using them.
The barrier should have been fixed firmly to the floor but was installed incorrectly. So when the young girl swung on it, it toppled over causing the serious injury which led her to miss eight weeks of school and left her with a permanent scar. In court, Arcadia admitted breaking health and safety laws, and has since put processes in place to reduce the risk of such an accident happening again.
If you are planning changes to your retail space, are opening a new store or just think your staff may need some extra training, contact us for expert health and safety support.
Maintenance procedures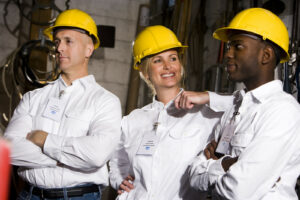
Failing to design an adequate process for maintaining machinery and checking it’s operating safely is a reason for HSE prosecution should an accident occur.
This spring, two waste companies were each fined tens of thousands of pounds for accidents which resulted in severe limb injuries. Parallels can be drawn because the injuries were inflicted when workers were trying to remove blockages and waste material from machinery.
In the first case, the worker had his hand crushed between a conveyor belt and a drive roller. A few weeks earlier guard plates had been removed. A main part of the prosecution was that there were no adequate procedures for checking guard plates were in place. Additionally, adequate training for using the machine and suitable supervision of operatives had not been provided.
In the second case, a worker fell three metres into a compactor chamber, activating the ram which crushed his legs. He had climbed into the infeed hopper and jumped up and down on a blockage with a colleague. When it cleared, he fell through with it. In particular, the HSE noted that there was no safe system for isolating the system from power when dealing with blockages.
For a review of your maintenance procedures, get in touch.
Safeguarding record-keeping
in schools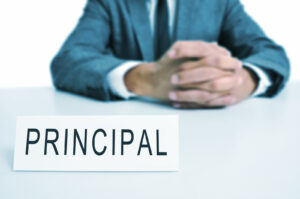
Adequately documenting procedures and keeping records are often an essential part of complying with health and safety law. In schools, this is particularly sensitive. And also, more likely to be publicly exposed as inadequate if you are not doing it properly – because of the routine Ofsted inspections and ratings.
An independent school in Yorkshire had to accept the bad PR consequences of this earlier in the year, when they were stripped of their “Outstanding” rating and declared “Inadequate”. Among other things, safeguarding was found to be ineffective and they had not met the standards for ensuring all necessary checks were carried out on adults working in the school.
Whilst apologising and confirming the issues had been addressed, the head teacher explained that the safeguarding issues related to record checking and keeping, and that safety and security of pupils was not directly put at risk.
Away from this specific case, and aside from the fallout from Ofsted reports and the potential to employ someone who would do harm to children, how else could poor record checking/keeping impact health and safety in schools? One example is in first aid.
If you don’t have a record of which team members are qualified first-aiders, you’ll lose track of when certificates expire and when staff with the qualification leave. This will make it likely that you don’t comply with your own first aid policy.
If you need help independently reviewing your record-keeping and checking procedures call The H&S Dept and one of our experienced local consultants will help.
Myth busters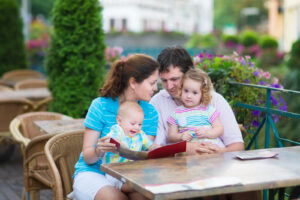
We like to wrap our children in cotton wool to protect them from danger, and very often from themselves. Most of the time this is entirely sensible and helps to prevent harm. But sometimes people go too far. Or businesses give health and safety a bad name by claiming a rule is because of H&S when in reality there’s a different underlying reason.
Sock it to ‘em
More cotton socks than cotton wool, but a soft play centre insisted that all children wear socks for health and safety reasons. While there is a public health need to cover feet infected with warts and verrucas, there’s no health and safety law mandating that socks are worn in soft play centres by all. The sock policy may meet this need, but it’s not specifically a health and safety requirement.
Don’t be a dummy
A café manager’s prohibition of baby’s dummies forced a family to leave prematurely. As with the case of the socks, the ban was blamed on the catch-all term health and safety. You can probably guess that there’s no health and safety legislation which stops babies being pacified with dummies in cafés. Digging deeper it was the café’s own strict internal food hygiene rules behind the ban. Better to just say that to begin with.
Is your work equipment
fit for purpose?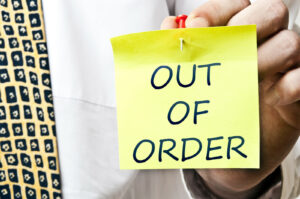
Failing to stay on top of seemingly innocuous maintenance issues on your premises can lead to tragic outcomes. That was the case at a Scottish care home, when a failing door lock led to the death of a resident.
After going missing, the resident was found with fatal head injuries at the bottom of a staircase leading to a boiler room. The staircase was kept off limits by a locked door, but the locking mechanism did not always work.
The death and a £60,000 fine show why even minor snags should not be left to lie. The technical breach was of Regulation 4(3) of the Provision and Use of Work Equipment Regulations 1998. This places a duty on you to ensure that equipment at work is suitable for the reason it is provided.
If you operate a care home and have concerns that your staff may not be carrying out the necessary control