Take the wheel on managing
moving vehicle risk at work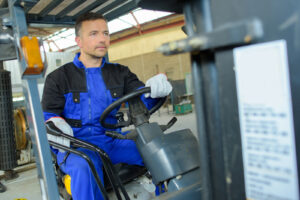
Managing the risk of moving vehicles at work is not something that every business has to contend with. But in warehouses, large retail stores, and airports, for example, it is a key area of health and safety. Poor procedures and systems of work present risks to the employee and customer alike. As an employer, you are legally required to be aware of such risks and take steps to eliminate or reduce them.
Much of this is governed by general health and safety legislation such as The Health and Safety at Work Act 1974. But be aware that there may be more specific legislation to consider too, including the Lifting Operations and Lifting Equipment Regulations (LOLER) 1998.
A moving vehicle risk assessment is essential to build a clear picture of where vehicles are, why they are there and what they are doing. This will help you identify potential vehicle hazards so you can take mitigating action.
Every year there are over 5,000 incidents involving transport in the workplace. And around 50 of these are fatal, so the risk is very real.
Common types of accidents involving moving vehicles include: people being struck or run over by a vehicle, people being hit by something falling from a vehicle, people falling from vehicles and vehicles overturning.
A court case following the death of a worker who walked in front of a moving lorry was recently reported on. While the driver had checked his mirrors, he did not see the employee and moved forward resulting in the fatal injury. The grain store company where the accident occurred was fined £180,000, as well as having to pay costs of £20,000.
In this instance the HSE found that pedestrians could not move safely around the site, as they had not provided measures to prevent employees walking into areas where large vehicles were moving. The company’s failure to implement simple H&S measures was cited as the cause for this avoidable incident.
Stop such potential disasters before they occur by managing the risks of workplace transport. Good practice measures include:
● Keeping people and vehicles apart
● Having clear site rules which are communicated to all staff members
● Avoiding the need to work at height on vehicles
● Ensuring your employees only operate vehicles when authorised to do so.
If you need help carrying out a moving vehicle risk assessment, or think your staff may need some extra training, contact us.
Is your care home heatwave resilient?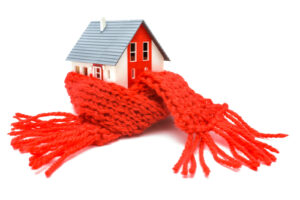
If you own or manage a care home, how well prepared are you and your staff for rising temperatures this summer? A study of four care homes found the heating was left on 24 hours a day, even during the summer months. And in a previous major heatwave, back in 2003, care home deaths related to heat increased by 42% that August.
“Heatwave resilience” is a term being used by MPs after last summer’s heatwave, to describe the best practice care homes should be seeking. Long-term trends suggest that UK summer temperatures are rising. So there is likely to be a smaller margin for error in managing this risk as the years pass. You’ll want to look at how temperature is controlled with both heating and cooling systems. Consider also the hydration and nutritional requirements of the people under your care during extremes of temperature.
Warning signs, aside from the obvious increase in temperature, could include a rise in incidents of urinary tract infections, dizziness and falls. Heatwave resilience is sure to move up the agenda of the Care Quality Commission (CQC) when they are inspecting care homes for safety and the effectiveness of their care. Regularly carrying out a heat risk assessment not only feeds into delivering the highest levels of care, but also helps you stay compliant with regulations.
If you operate a care home and have concerns over your staff’s readiness for a heatwave, or need help carrying out a heat risk assessment, get in touch with us today.
Extracurricular work in schools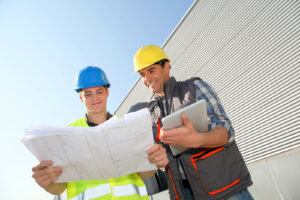
Summer holidays are the time when schools get major building work done. Although there won’t be children around, you’ll still want to ensure health and safety regulations are followed if you have responsibility in this area.
Your schedule of work may range from a few thousand pounds for play equipment, to hundreds of thousands of pounds for major developments like roofing works. However big or small your project, you’ll have responsibilities under the Construction (Design and Management) Regulations 2015. Classified as a client, you’ll be responsible for ensuring your project is suitably managed, considering the health and safety of anyone who might be affected.
Building activities over the summer holidays aren’t quite “business as usual”, so don’t get caught out. There may be fewer or no children about, but ensure you plan for other people on site, including contractors and your teachers coming in to prepare their classrooms for next year.
Make sure your shop is
hot on fire regulation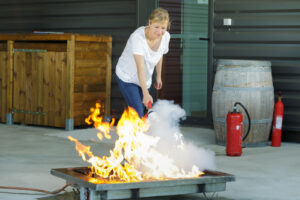
A member of the public has been banned from every branch of a popular homeware store in the UK, after arguing in the carpark with a manager that the store breached health and safety laws. The customer, Derek, raised concerns over the fact that staff were locked into the store for 15 minutes at the end of the day. He also criticised the store’s covered fire extinguishers.
Despite his ban, Derek raised some important fire safety issues. If you own or manage a shop, you’ll want to make sure you’re aware of them. The Regulatory Reform (Fire Safety) Order 2005 stipulates that emergency doors must not be locked if they cannot be easily and immediately opened in an emergency. It also states that they must be kept clear at all times.
It was reported that the front door of the store was its main fire escape. The locking of fire doors presents a clear obstacle to an immediate exit. If you want to signal that your shop is closed for business, but still have employees inside, consider hanging a closed sign or have an employee at the front door to turn customers away, or specifically to open it in the event of an emergency.
When it comes to fire extinguishers, you must ensure they are maintained and ready for immediate use. The regulation doesn’t mention covers specifically, but they should be fitted properly (for example not used to prop open a door), and easily accessible.
HSE Myth Busters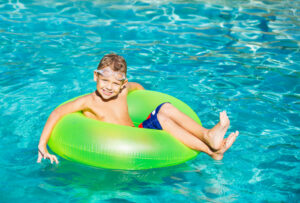
When we are off on a plane for our summer holidays or relaxing in a pool, being denied a reasonable request due to health and safety will not cut the mustard. Here are two examples of summer holiday businesses which did that and earned a place on the HSE Myth Busters panel. The lesson is: don’t blame management decisions on health and safety without a good explanation.
Something to chew on
One adult passenger was forced to put up with popping ears after an airline refused to provide boiled sweets on the grounds of health and safety. They claimed that because children could choke on them, they were banned outright. While it is sensible to avoid giving hard sweets to young children, there is no health and safety legislation that prevents the provision of boiled sweets on flights.
Sink or swim
One swimming pool banned inflatables and other items that people enjoy in swimming pools on the grounds of health and safety. Health and safety law does apply to the management of public swimming pools but does not explicitly ban these items. They may have had a good reason, like impeding a lifeguard’s ability to have complete sight of the pool, but it would have been better to say this rather than making health and safety legislation the killjoy.