Are you taking fire safety seriously
enough in your school?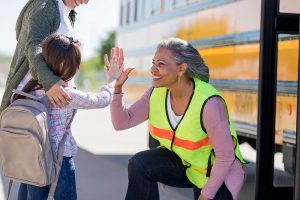
A leading education insurance provider recently surveyed 1,000 UK schools to see how they’d cope with a fire.
The results were not overly promising. Two-thirds of schools across England don’t have a proper system for dealing with fire. And only 5% of schools received an ‘excellent’ rating in the survey. Scottish schools fare better with about 30% being rated excellent.
In Scotland, sprinklers are a legal requirement in the new and major refurbished schools. But since 2011, 673 UK schools opened and only 15% of them had sprinklers installed. The insurer is pushing the government to introduce legislation so that sprinklers become an integral part of all UK schools.
The obvious substances most likely to cause a fire are unlikely to be found in schools. However, the less obvious, such as packaging materials or dust from flour, sugar, or wood, are very common.
The study also outlined five main risks. These were:
- Shortcomings in fixed fire protection
- Deficient fire detection systems
- Arson
- Modern construction procedures and how combustible a building is
- Smoking controls and general housekeeping
There are more than 1,000 school fires each year. The risk to health and life speaks for itself. The average financial cost is almost £3million for more serious incidents, but there is an educational cost too. Premises could be closed for extended periods of time while repairs are carried out. Classes are disrupted as they are moved to alternative premises. And groups who usually use the school out of hours are unable to.
The good news is that the majority of fires can be prevented.
When it comes to overall fire safety, The Regulatory Reform (Fire Safety) Order 2005 looks after England and Wales. Generally, local fire and rescue teams are responsible for ensuring the majority of buildings abide by this legislation. In Scotland the Fire (Scotland) Act 2005 brought in changes to fire safety law and repealed previous fire safety legislation. And in Northern Ireland it is The Fire Safety Regulations (Northern Ireland) 2010.
Fire drills and safety risk assessments should be carried out regularly. Both are mandatory for UK schools. A health and safety risk assessment adopts similar methods, so they can either be conducted together or as separate assessments. Beyond this, it may be time to review your fixed fire protection.
The survey suggests many schools are not as prepared as they should be. If this includes you, it’s what you do next that counts. If you need to review your risk management procedures or fixed fire protection, but don’t know where to start, we can help. So give us a call.
Unclear allergen labelling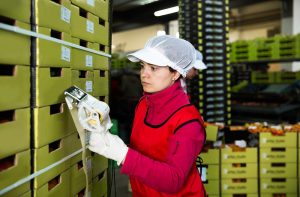
Sometimes a simple case of customer miscommunication can result in a simple mistake. But occasionally, the consequences can end in tragedy.
You’ll probably have seen in the news that a teenager paid with his life after reading from a restaurant’s misleading menu. He chose the chicken burger. Neither the menu nor staff had made it clear the burger was coated in buttermilk. Milk is one of the 14 main allergens.
An hour later, he was dead. In an earlier high-profile case, a fifteen-year-old girl, Natasha, also died after suffering a fatal allergic reaction from a sandwich.
New laws are set to be introduced to provide further protection. Under ‘Natasha’s Law’, mandatory allergen labelling will be extended to cover food prepared, packed and sold all on the same premises. Previously this “pre-packed directly for sale” food was exempt from allergen labelling.
The Food Standards Agency (FSA) is clear that anyone eating out or ordering takeaway must have access to written allergen advice. This might be through a menu or at the very least, written instructions detailing how they can find out. Relevant legislation includes the Food Safety Act 1990 and the European Food Information to Consumers (FIC) Regulation 1169/2011.
If you work in the food industry, we can help you undertake a risk assessment and develop effective training. We’ll ensure you comply with the law and even go beyond it, to keep your customers safe and protect your reputation.
Every breath you take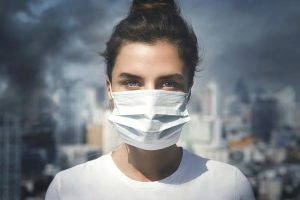
Have you heard of ‘sick building syndrome’?
It might be a headache, runny nose, or throat irritation, but you’ll only get it while in a certain building. It’s usually an office and one of the causes is poor air quality.
Some workplaces have a legal requirement when it comes to ventilation and extraction systems. But even those that seem safe may be riddled with hidden pollutants including fungal spores, carpet fibres and photocopy residue.
Without proper cleaning, maintenance and ventilation, harmful particles are likely to build up.
If the building is older, there may be inherent issues with heating, ventilation, and air conditioning.
For instance, if you have an air conditioning system which isn’t properly maintained, it may produce daily swings in temperature. The system could create extreme levels of humidity and bring in chemical pollutants and dust particles from the outside, all of which can contribute to illness.
New partitions may offer more privacy, but they can also encourage stagnant air and pollutants to build up. So it’s a good idea to consider air quality when having work done.
A recent YouGov survey found that nearly 70% of office workers consider the air quality detrimental to their productivity and well-being. Pollution outdoors is already linked with respiratory tract infections and lung disease. What could the long-term effects of poor indoor air quality be?
It’s not always easy to identify the problem. Try simple things first. You may even be able to tackle a pollutant at source. Well-placed ventilation or advanced carbon-activated air purifiers can certainly help.
If you have an air-quality problem, talk to us about getting to grips with it and arranging an occupational hygienist to check the correct standards are being met.
HSE Myth Busters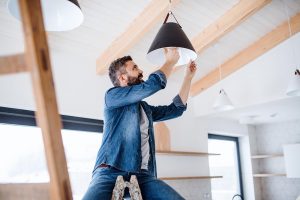
Most people are not fans of repair and maintenance, but it does prevent things from sliding into disrepair.
Whether its through laziness or a simple misunderstanding, no business or institution should make a scapegoat of health and safety as an easy excuse. But unfortunately, it’s still being given a bad name. Today we’ve got two great examples we dug up from the HSE Myth Busters.
Light bulb moment?
How many handymen does it take to change a lightbulb?
None, apparently, because health and safety is stopping anyone but a qualified electrician from doing it. At least that’s what a property management company said in a bid to protect themselves from a negligence claim. It doesn’t! And unhelpful attitudes like that simply obstruct necessary work being done.
On the verge of despair
As a newspaper reporter drove through the South Downs National Park, she could hardly believe the piles of litter at the side of the road.
Of course, the council chucked her an excuse around health and safety. Understandably, the reporter was shocked the regulation didn’t cover British wildlife.
The truth is – there is nothing stopping a council from clearing verge litter provided they ensure traffic risks are properly managed. In the end it would have been much better for them to have admitted their real reason, whatever that may have been.
Time to safety-check your equipment?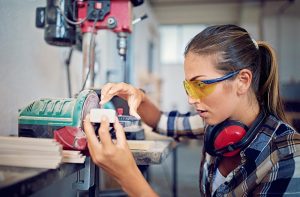
Usually, hindsight can be a wonderful thing.
But what if there are implications for health and safety?
Well then, it’s always better to prevent than try to fix it later on. The number of workplace injuries owing to unsafe equipment suggests that it’s worth seeing whether safety-checking needs to go up your to-do list.
In one recent HSE prosecution, for example, a furniture manufacturer learned the hard way that they should have placed a guard on their drilling machine. They not only landed a £14,000 fine, but the poor worker involved lost two of his fingers.
Technically speaking, they breached Regulation 11(1) of the Provision and Use of Work Equipment Regulations 1998. This legislation is designed so that you, the employer, can make sure your workplace equipment is fit for purpose and most importantly, safe to use.
If you manage a company that operates potentially dangerous machinery, ensure you conduct regular equipment inspections. If you need outside help setting up a review process, get in touch.